ESCATEC staff, trained on the OEM’s computer system, effectively worked on behalf of our client. Our staff acted as an extension of their logistics team to ensure orders received up to 2 PM local time in the Czech site were shipped that day, or those received after were shipped the next day.
We also managed a portfolio of around 2,000 spare stock-keeping units (SKUs) or different components on behalf of the customer. From these units, ESCATEC could ship around 20,000 spare items, of varying combinations depending on demand, per month.
This meticulous process enabled a smooth production run for every product manufactured, from the initial order to the final product, without the OEM ever having to see or touch their own product. With this approach we were able to ship roughly 800 finished machines per month.
This is the ultimate in end-to-end manufacturing solutions. As a result, the OEM could focus on designing its next cutting-edge product while expanding market share without any distractions associated with manufacturing, order fulfilment, or logistics.
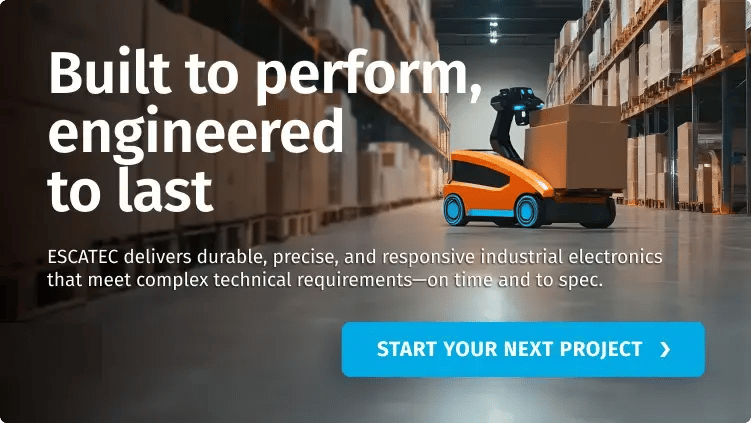