Pressure from consumers. Pressure from regulators. Pressure from a planet running dry of natural resources. The drive to manufacture more sustainable electronic products is not just a PR mission anymore. Designing more ‘circular products’ is becoming an ethical and regulatory imperative. And it will soon be an economic necessity. What skills and knowledge do you need in place to ensure designs for electronics products are optimised for sustainability throughout their entire lifecycle?
What is Design for Sustainability?
Also known as Design for the Environment (DfE), Design for Sustainability is an industrial methodology ensuring products are specified for maximum efficiency; extending their lifecycle, recyclability and minimising their polluting potential.
Product designs can 'lock in' long term environmental damage
The European Commission’s Sustainable Product Policy says that up to 80% of a product’s negative impact on the environment is locked in at the design stage. And it’s easy to see why. After all, every time we make a material choice or specify the use of a certain component in a product there are inevitable consequences for recyclability, assembly and end-of-life disposal.
Just think about the objects you use every day. Is your toothbrush made from plastic or bamboo? Can you replace the battery on your iPhone? What will you do with your computer monitor when it stops working? Can it be usefully mended or the parts disassembled for ease of recycling? Those decisions were made as the designs were finalised and they can have long-term consequences for the planet.
What does DfE mean for EMS providers?
DfE analyses the potential for environmental damage within the entire product life cycle through:
- Procurement decisions
- Material choices
- Fabrication methods
- Repairability options
- End-use cases (including operational efficiency and end-of-life )
DfS systematically overhauls design and manufacturing specifications to find ways to optimise the products’ longevity and minimise their polluting potential.
DfS aims to support the principles of the 'circular economy', which looks to align commercial and environmental goals through more reuse and regeneration:
"A circular economy is an industrial system that is restorative or regenerative by intention and design. It replaces the end-of-life concept with restoration, shifts towards the use of renewable energy, and eliminates the use of toxic chemicals which impair re-use and return to the biosphere. Additional benefits represent the increased sustainable economic growth and the creation of new business opportunities and innovative, more efficient business models of producing and consuming."
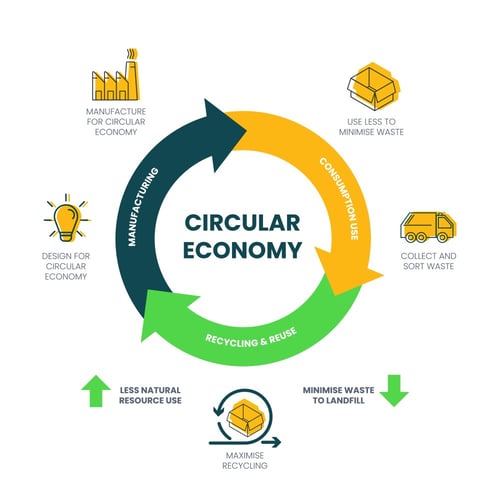
What are the principles of sustainable design an EMS can help with?
These are key areas that can be addressed by manufacturing specialists at the design stage to ensure products are built for longevity :
- Dematerialisation
- Increased modular design
- Fighting built-in obsolescence
- Energy use
- Limiting long-distance sourcing
- Choosing simulations in design
Dematerialisation
The United Nations Environment Program (UNEP), encourages businesses to focus on “the reduction of total material and energy throughput” in manufacturing.
Much of the DfX tool kit can be deployed to help with this goal. DFMA (Design for Manufacturability and Assembly) looks to analyse a products’ functions (i.e. what the customer actually wants from them) to combine or eliminate components where possible. It also looks to reduce process steps to save on manufacturing time and energy by reducing design complexity.
Dematerialisation can make a product cheaper for the consumer by simply being less expensive to make, but making it lighter or smaller can also reduce transportation costs and carbon footprint later down the chain. For example, a 10% weight reduction in the weight of vehicles can generate a 6% improvement in fuel economy across its lifecycle.
Modular design
Choosing modular designs for electronic products has obvious environmental benefits:
- Modules can be replaced without changing anything else on the product.
- Modular design enables quick and easy upgrades (increasing lifecycle)
- Replacement of worn parts (which can then be recycled)
- Flexibility in use, as the way customers use products can change over time.
- Easy and quick servicing and maintenance of products (reduced time in workshop/energy savings)
- Designed for disassembly (easier end of life disposal/recyclability)
Fighting built in obsolescence
Planned obsolescence has long been the unspoken shame of the electronics industry. From light bulbs to Apple phones, shorter life spans have often been built into tech products to keep cash tills ringing.
But unplanned obsolescence can happen simply due to a lack of visibility around component and material availability as products are designed and specified away from manufacturing expertise.
Working with manufacturing specialists with the right systems in place, can alert designers to which components are about to be discontinued or increase in price to unsustainable levels, while offering more eco-friendly, sustainable alternatives.
Energy use
What power source will your product use? Does it have to be mains powered or can it use renewable energy sources? How energy efficient will the product be? There are regional regulations around energy consumption and choices that you may have to bear in mind to ensure your product can be legally sold. Choosing a manufacturing partner with a global perspective and proven sustainability credentials will help you make the right decisions to minimise the polluting potential of your product as it is operated.
Limit or eliminate long-distance outsourcing
The trend for re-shoring is gathering pace. Regionalisation is being made possible by digital advances, for example, cloud control of production plants and additive manufacturing. Localised raw material and component sourcing can all help eliminate reliance on polluting international supply chains. As recycling initiatives for rare elements vital for electronics manufacturing increases, these aims are becoming more achievable.
Choose simulations for prototyping and design
Prototyping using computer simulation can be more environmentally friendly than going through successive real-world iterations. It can ensure tolerances are calculated precisely and different manufacturing scenarios are worked through before time and materials are wasted in physical experimentation.
Using CAE (computer-aided engineering) software, designers can analyse individual parts as well as entire assemblies for stresses, defects, impact, heat and fluid flow without having a physical prototype. They can even simulate tooling for manufacturing processes deciding how assembly lines can best be optimised.
Legislation and regulation tightens
In the face of public pressure and dire climate and pollution warnings, governments around the world are imposing legislation to force change upon industry . Many environmental safeguards are already built into existing regulations and good manufacturers will attend to these as part of their quality management systems:
- ROHS (Restriction of Hazardous Substances Directive),
- REACH (Registration, Evaluation, Authorisation and Restriction of Chemicals)
- WEEE (Waste Electrical and Electronic Equipment recycling) standards
But as net zero targets loom there will be more regulation, and more sanctions imposed upon industries who do not meet required standards. For example, more than 30 companies have already been issued with fines by the UK Environment Agency as part of efforts to reduce greenhouse gas emissions.
Pressure from customers and pressure from regulators is increasing as the evidence of dramatic climate change and environmental destruction stoked by manufacturers stacks up around the world.
Taking steps to design for sustainability is going to be a commercial, as well as an ethical imperative as we move forward into an uncertain era of widespread global climate change.