When you think about what makes a ‘good’ electronics assembly, what are the most common expectations that come to mind? If the assembly works as intended then surely that indicates a certain level of acceptability, right? But what about the product's longer-term reliability? And what if you'd also like it to 'look good' too?
A Printed Circuit Board Assembly (PCBA) is a surprisingly complex thing. There’s the printed circuit board itself with all its material and finishes, its various components, and the solder that holds everything together. Within that, there’s also a fair amount of scope for things to be 'good', or 'bad', or somewhere in between.
To assist EMS providers, OEMs, and other stakeholders in the electronics industry to agree on what "good" looks like, the IPC has developed a comprehensive set of standards over the years that serve as a universal point of reference.
What is IPC-A-610?
IPC-A-610 is the globally recognised standard for assessing the acceptability of electronic assemblies. Developed by the ‘Association Connecting Electronics Industries’ (IPC), it provides detailed criteria for visual inspections, workmanship standards, and quality assurance in PCBA production. It’s just one of a family of standards covering almost every phase of the PCB manufacturing process.
The standard is divided into three classes—Class 1, Class 2, and Class 3—each catering to different reliability and performance needs.
What is IPC-A-610J?
IPC-A-610J was the latest version of the standard and was officially released in April 2024. It represents a significant evolution in electronics assembly quality requirements. The update was necessary to address the increasing complexity of modern electronic assemblies and emerging manufacturing challenges.
Key changes in the J revision include new guidelines for conformal coating inspection, with specific clarification on voiding and bubbles assessment. It has also been substantially enhanced with new images to improve visual inspection guidance.
In addition, Section J include:
- Improved guidelines for solder joint evaluation
- Updated cleanliness standards to address modern flux residues
- Recommendations for enhanced training programs for inspection consistency
The three classes of IPC-A-610
Class 1: General electronic products
Class 1 of the IPC standard is the lowest of the classes, and so the most 'lenient' when it comes to making allowances for potential defects.
When we think of the functionality of the electronics assembly within a simple toy, for example, the PCBA is likely to be hidden well away inside the body of the item so the quality of the solder joints or component positions may not be such a high priority.
The product is also likely to be manufactured to very tight margins (read "as cheaply as possible") so as long as the item still functions as expected (and its operational life sits within an acceptable time-frame) then that's probably going to be sufficient.
Class 2: Dedicated service electronic products
Class 2 strikes a balance between cost-effectiveness and reliability. It is ideal for products that require extended service life but where controlling functions are not life threatening or mission-critical. For example:
- Industrial electronics
- Automotive components
While some imperfections are tolerated (e.g., slightly misaligned surface-mount components), these do not compromise electrical or mechanical performance. Class 2 is often the most requested standard due to its practicality and affordability.
Class 3: High-performance electronic products
Class 3 represents the highest standard of quality and reliability. It is reserved for applications where failure could result in severe consequences, such as:
- Aerospace systems
- Medical devices
- Military equipment
Assemblies meeting Class 3 standards must adhere to stringent inspection criteria across all aspects of production, including laminate selection, solder joint integrity, cleanliness, and inspection processes. Achieving this level of precision often involves additional costs due to ruggedisation needs, slower production speeds, higher scrap rates, and rigorous inspections.
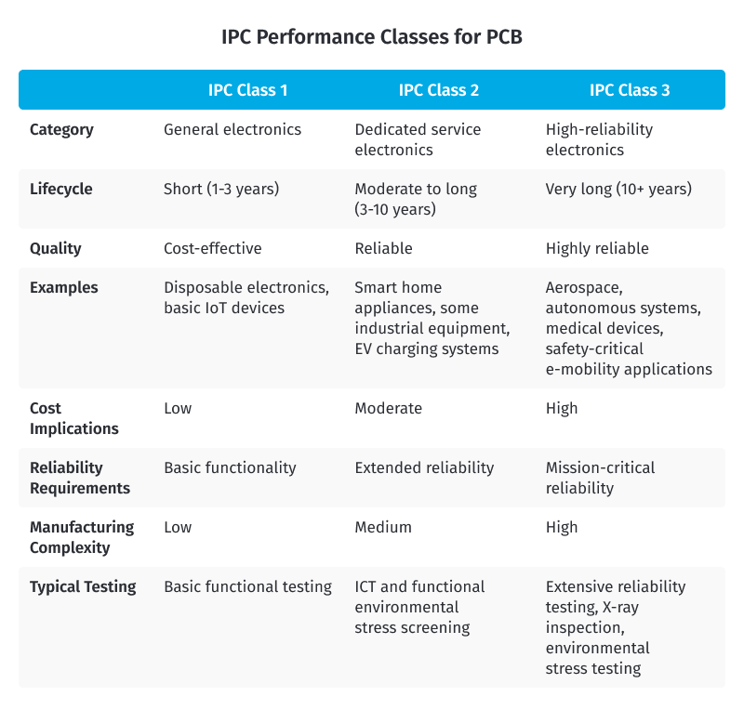
Working with your EMS partner
Many would argue that a reliable EMS provider will always aim to manufacture the products they build to the Class 3 standard, regardless.
Any EMS provider that is genuinely serious about compliance is also undoubtedly going to have well-established internal training programmes to promote awareness within their manufacturing facility.
Ideally too, this compliance is likely to extend not just to the inspection of the end products, but also to monitoring every process of the build.
The best way to achieve this, and to maintain the standards required, will be for them to appoint in-house IPC trainers who will themselves be externally re-certified.
It should be remembered that IPC certification is not a one-time achievement. Most require renewal every two years to ensure continued competency and awareness of updated standards. This ongoing process includes:
- Periodic audits
- Continued education
- Assessment of practical skills
- Review of any standard updates or changes
In the majority of cases, the IPC-A-610 standard will suffice. But there may also be situations where an OEM prefers to produce their own criteria - to either enhance, or to replace, the existing standard.
If you do choose to create your own set of guidelines, then it will be important to ensure that your EMS partner is crystal clear about your expectations from the outset. So ideally, you should reference your specific criteria on every Request for Quotation (RFQ) or purchase order that you submit.
Editor’s note: this post was originally published in April 2019, and updated in January 2025 for accuracy.