When and how will OEMs start to see the full benefits of AI across the manufacturing cycle? In our latest blog, Peter Gutschi, member of the ESCATEC board of directors, explores the potential long-term, transformative effects of AI in the EMS industry.
AI is one of the most profound things we're working on as humanity. It's more profound than fire or electricity,” said Alphabet Inc. CEO Sundar Pichai.
Is he right?
Fire made all human tech progress possible. It led to metal tools, steam, electrification, and (by extension) the IT revolution and the birth of AI. It’s taken roughly 6000 years for that spark of tamed fire to take us from the Iron Age to Industry 5.0.
But AI promises to accelerate future discovery and industrial innovation at a rate we’ve never seen before.
And the manufacturing sector is no exception.
AI is expected to boost global manufacturing productivity by up to 40% by 2035.
Source: Accenture
Enter generative AI
As McKinsey concluded in 2023, LLMs (Large Language Models) are ushering in a new era of technological progress.
Generative AI is… pushing technology into a realm thought to be unique to the human mind: creativity.
Source: McKinsey
In other words, generative AI is not just sucking in and rearranging pre-existing information like older AI applications but minting original ideas based on gathered insight, analysis, and its own learning from massive datasets. And it can do so in seconds.
To take just one example, in the bioscience realm, AI platforms powered by machine learning have already collapsed the discovery time for certain novel cancer treatments from decades to months.
With these self-learning AI models, it’s possible to imagine product development and manufacturing cycles, prompted by humans but refined, managed, and automated by computers from beginning to end.
Companies using AI in their product development processes can reduce time to market by 20-40% and cut development costs by 20-30%.
Source: Virtasant
Here’s an overview of some of the exciting possibilities of AI and associated innovations happening in the electronics manufacturing industry right now:
8 benefits of AI for manufacturing; powering end-to-end product development cycles
1. Brainstorming new product ideas
AI is already being used by major companies to project trends and generate innovative product ideas:
- Suzuki uses AI to fuel the prioritisation of product improvement and development initiatives.
- Netgear uses AI to detect abnormal customer sentiment, generating millions of US dollars of value in the process.
- Samsung uses AI to analyse consumer trends, market data, and user feedback to generate innovative product concepts for their electronics lineup. Their AI system processes vast amounts of information from social media, product reviews, and sales data to identify emerging consumer needs and preferences.
2. Design and documentation
AI tools are also being used by manufacturers to generate various critical assets in the product development cycle:
- Business cases, product specifications, designs, computer coding, and quality documentation are already being AI-generated by many companies.
- Design visualisation tools like Midjourney and DALL-E are used to render diagrams and blueprints instantly.
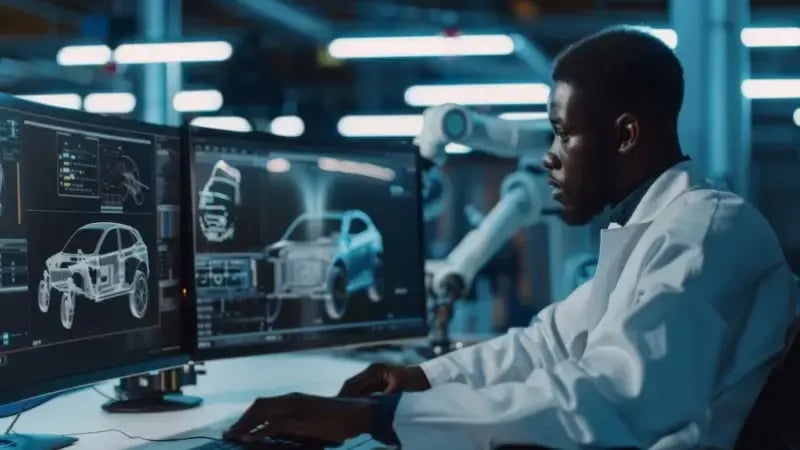
- Designs are being prototyped and tested virtually, with physical prototypes, then 3D printed on demand.
3. Production planning
When it comes to production planning, AI-powered tools are transforming processes by enhancing efficiency, which is, in turn, reducing time to market and optimising resource use across industries:
- Predictive analytics: AI tools can forecast potential failure modes, optimise material usage, and improve production reliability. By predicting and mitigating potential issues before they arise, these tools streamline production timelines and minimise costly disruptions.
- Adaptability in manufacturing: DarwinAI’s VQI systems (Visual Quality Inspection) are specifically designed to adapt to changes in PCB manufacturing, such as material or component substitutions, without the need for extensive reprogramming. Leveraging generative AI, these systems quickly learn to identify new or alternative components, ensuring consistent quality control even when manufacturing variables change
- Luminovo’s AI platform enhances PCB planning capabilities by providing design-to-source optimisation, real-time BOM insights, and automated sourcing. By enabling faster component procurement and accurate cost estimation, Luminovo helps manufacturers streamline production planning from the earliest stages, reducing time to market and improving resource allocation.
4. Supply chain optimisation
In the supply chain, AI algorithms are optimising inventory management, demand forecasting, and logistics, helping businesses handle supply chain challenges more effectively, minimising disruptions and improving overall resilience.
- Omnics’ AI system aggregates manufacturing and supply chain data from various systems, providing end-to-end visibility around capacity, supply, demand, inventory, finance, product, freight, and after-sales.
- Sluicebox is an AI powered platform that calculates the carbon footprint of electronic components in the supply chain. Their API allows for integration with existing systems, to help manufacturing and procurement teams make more eco-friendly buying decisions. They also partnered with Luminovo to offer this feature on their platform.
5. Process automation
AI-powered robots and cobots are improving manufacturing processes on the factory floor:
- Companies like Bright Machines and ABB offer AI-powered robots that can handle repetitive tasks such as assembly, soldering, and quality control.
- Bright Machines offers advanced AI-driven micro-factories that automate tasks like assembly and inspection. Their modular, scalable approach enables manufacturers to optimise production lines for efficiency and flexibility. By combining robotics, computer vision, and software, Bright Machines’ solutions make it easier for agile companies to adapt to changing production demands.
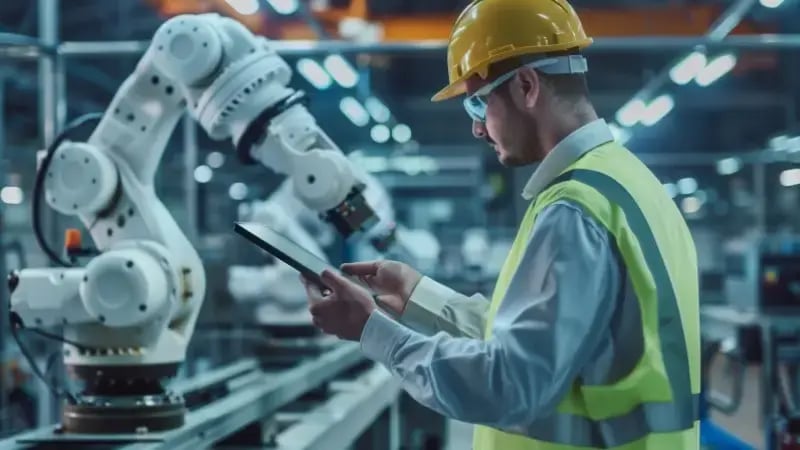
- ABB specialises in AI-powered industrial robots and collaborative robots (cobots) designed to streamline complex manufacturing processes. Their robots can handle a wide range of tasks, including assembly, welding, and precision quality inspection. What sets ABB+ apart is its focus on human-robot collaboration, enabling robots to work safely alongside human operators while enhancing flexibility on the production line.
6. Predictive maintenance
Technology like sensor data is being used by AI tools to analyse and improve equipment performance:
- Siemens’s Senseye Predictive Maintenance platform uses AI to predict potential machine failures and maintenance needs on production lines. It has already helped to reduce unplanned downtime by up to 50% while increasing maintenance staff productivity by up to 30%.
- Senseye draws in multi-language data from various international sites, helping predict and prevent manufacturing issues using shared data. They have developed a user-friendly interface which allows engineers to seek preventive maintenance advice directly from the vast datasets within.
7. Quality control
In electronics, AI-powered machine vision systems are enhancing product quality across the industry:
- Inspekto, another Siemen’s product, is an AI-based visual inspection system designed for manufacturing quality control. It offers plug-and-play automation, requiring minimal setup with no specialised expertise. It enables fast, accurate, and affordable quality checks, ensuring that components meet stringent quality standards without requiring human inspectors to check each part manually.
- Cybord is an inspection system that leverages AI to ensure the quality, authenticity, and traceability of electronic components. Their system performs real-time analysis of components on assembly lines using machine learning and big data to detect counterfeit or defective components, reducing recalls and improving manufacturing efficiency.
8. Post-market activities
AI facilitates the comprehensive analysis of product performance and customer feedback, helping businesses prime assembly lines for next-generation models with minimal human input:
- Large volumes of usage data and customer feedback are already being collected and analysed from various customer service and market surveillance inputs.
- Companies are using AI to flag non-conformances for investigation and monitor customer satisfaction in real-time.
- Flinn.ai optimises post-market surveillance (PMS) for medical device manufacturers with automated safety database monitoring, intelligent literature analysis, and AI-enhanced complaint data processing. The platform gathers and filters information from multiple sources, identifies vigilance cases and complaint trends, and generates MDR-compliant reports with a single click.
Already, we are seeing different EMS companies using AI in various ways to offer a competitive advantage to their customers.
But what will be the impact on job roles and skills?
Change will be profound.
Routine tasks will be automated, leading to a decline in certain roles.
However, there will be a much greater need for a highly skilled manufacturing workforce with a broad range of experience and technical skills, such as:
- Building resilient and eco-friendly supply chains
- Advanced data analytics
- Leverage of AI and machine learning (ML)
- Software development
- Microelectronics and robotics
Workers will collaborate more fully with robots and AI systems, and human roles will focus more on problem-solving, creativity, and adaptability.
Existing workers will need to acquire new skills. Successful training will need to focus on AI-literacy, programming, and understanding of the new AI-driven systems we have explored above.
Soon, there will be intense competition for those with these skills in the employment market.
What’s standing in the way?
Many EMS companies are already integrating AI into their processes, and those workers exposed to these systems are adapting fast.
But there are serious obstacles to negotiate, too.
As Adam J. Fleischer of Altium points out in his recent analysis of the impact of AI on electronics manufacturing:
“While AI can lead to significant cost savings in the long run, the upfront costs of implementing AI systems can be a blocker for smaller manufacturers.”
Plus, there are considerable challenges ahead in finding ways to validate the workings of ‘black box systems’, as they take more responsibility for designing, building and testing potentially lethal devices.
IBM’s Global AI Adoption Index found that 56% of businesses using AI are not working to develop ethical AI policies, and 74% are making no efforts to reduce unintended biases.
Source: IBM
How quickly will AI transform the EMS sector?
The most significant push for AI adoption in the manufacturing sector will likely occur within the next 3 - 5 years. As AI matures, organisations will need to restructure roles as learning and development programs accelerate.
Companies will need ‘all hands on deck’ to figure out how they can best use AI to design and develop their products. This includes working out where they can most usefully outsource to manufacturers with the equipment and big data needed to build products more efficiently and to the highest quality.
Additionally, they need to consider how they can harness new AI technologies to accelerate the pace of their production ideation, R&D and prototyping.
Companies that have implemented Kazien processes for continual improvement and have a collective road map for organisational change will be best placed to transform the quality and efficiency of their practice with AI.